Крутящий момент для резьбонарезных головок CNCM, формулы, советы
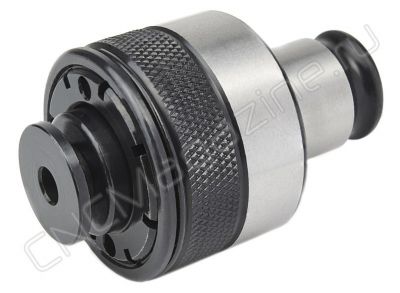
Содержание:
1. Предустановленный крутящий момент резьбонарезных цанг CNCM
2. Формулы по настройке крутящего момента для метчиков
3. Удельное усилие резания (Величина Kc)
4. Поправочные коэффициенты при износе инструмента
В таблице ниже указан предустановленный крутящий момент для резьбонарезных головок CNCM:
Размер резьбы |
Настроенный момент (nm) |
Размер резьбы |
Настроенный момент (nm) |
M3 |
0,5 |
M16 |
40,0 |
M3.5 |
0,7 |
M18 |
62,0 |
M4 |
1,2 |
M20 |
71,0 |
M4.5 |
1,5 |
M22 |
79,0 |
M5 |
2,1 |
M24 |
123,0 |
M6 |
4,2 |
M30 |
221,0 |
M8 |
8,1 |
M33 |
241,0 |
M10 |
16,0 |
M39 |
320,0 |
M12 |
21,0 |
M45 |
480,0 |
M14 |
35,5 |
M48 |
630,0 |
Заводские настройки:
Диапазон допуска M3-M10: ± 0,1 нм; M12-M22: ± 0,5 нм; M24-M48: ± 1 нм.
Увеличивайте крутящий момент по часовой стрелке и уменьшайте крутящий момент против часовой стрелки. Используйте динамометрический ключ.
Примечание: при поломке метчика необходимо отрегулировать крутящий момент, чтобы избежать экономических потерь.
Формулы по настройке крутящего момента для метчиков
Формулы расчета крутящего момента при резьбонарезании метчиками:
Об/мин:
Расчет крутящего момента:
Мощность:
Правильно установленный крутящий момент обеспечивает плавное нарезание резьбы. Для мелких шагов резьбы величину крутящего момента нужно рассчитать по формуле:
Mx = Mm√(Px/P)3
Mm – крутящий момент по таблице, Px – шаг резьбы, P – крупный шаг резьбы для данного диаметра.
Удельное усилие резания (Величина Kc)
Удельное усилие резания (Величина Kc) |
Сверление |
Фрезерование |
Резьбонарезание |
|||
k |
Kc1 |
z |
Kc |
|||
Группы обрабатываемых материалов |
Коэффициент обрабатываемости материала |
H/mm2 |
Коэффициент коррекции |
H/mm2 |
||
1. Сталь |
1 |
Электротехническая |
1,3 |
1400 |
0,18 |
2000 |
2 |
Конструкционная, в том числе цементируемая |
1,4 |
1450 |
0,22 |
2100 |
|
3 |
Углеродистая нелегированная |
1,9 |
1500 |
0,2 |
2200 |
|
4 |
Легированная |
1,9 |
1550 |
0,2 |
2400 |
|
5 |
Легированная, после закалки и отпуска |
2,7 |
1600 |
0,2 |
2500 |
|
6 |
Легированная, после закалки и отпуска |
3,4 |
1700 |
0,2 |
2600 |
|
7 |
Легированная, закаленная |
3,7 |
1900 |
0,2 |
2900 |
|
8 |
Легированная, закаленная |
4 |
2300 |
0,2 |
2900 |
|
2. Нержавеющая сталь |
1 |
Повышенной обрабатываемости |
1,9 |
1300 |
0,36 |
2300 |
2 |
Аустенитная |
1,9 |
1500 |
0,32 |
2600 |
|
3 |
Аустенитная-ферритная |
2,7 |
1600 |
24 |
3000 |
|
4 |
Дисперсионно-твердеющий сплав |
|
|
|
3100 |
|
3. Чугун |
1 |
С пластичным графитом |
1 |
900 |
0,26 |
1600 |
2 |
С пластичным графитом |
1,5 |
1100 |
0,26 |
1600 |
|
3 |
С шаровидным графитом |
2 |
1150 |
0,24 |
1700 |
|
4 |
С шаровидным графитом |
1,5 |
1450 |
0,24 |
2000 |
|
4. Титан |
1 |
Технически чистый |
1,4 |
900 |
0,2 |
2000 |
2 |
Титановые сплавы |
2 |
1200 |
0,22 |
2000 |
|
3 |
Титановые сплавы |
2,7 |
1450 |
0,22 |
2300 |
|
5. Никель |
1 |
Технически чистый |
1,3 |
1100 |
0,12 |
1300 |
2 |
Никелевые сплавы |
2 |
1450 |
0,22 |
2000 |
|
3 |
Никелевые сплавы |
2,7 |
1700 |
0,22 |
2000 |
|
6. Медь |
1 |
Технически чистый |
0,6 |
450 |
0,2 |
800 |
2 |
Бронзы и латуни на основе Sn |
0,7 |
500 |
0,3 |
1000 |
|
3 |
Бронзы и латуни на основе Zn |
0,7 |
600 |
0,32 |
1000 |
|
4 |
Высокопрочные бронзы |
1,5 |
1600 |
0,36 |
1000 |
|
7. Алюминий, магний |
1 |
Технически чистый |
0,6 |
250 |
0,22 |
700 |
2 |
Их сплавы, с содержанием, Si<0.5% |
0,6 |
450 |
0,18 |
700 |
|
3 |
Их сплавы, с содержанием 0.5%<Si<10% |
0,7 |
450 |
0,18 |
800 |
|
4 |
Их сплавы, с содержанием Si>10% |
0,7 |
500 |
0,15 |
1000 |
|
8. Пластмассы |
1 |
Термопластики |
0,6 |
1400 |
0,15 |
400 |
2 |
Термореактивные |
0,6 |
1400 |
0,2 |
600 |
|
3 |
Армированные |
1 |
1600 |
0,3 |
800 |
|
9. Твердые материалы |
1 |
Металлокерамика |
4 |
2600 |
0,38 |
>2800 |
10. Графит |
1 |
Технический |
- |
200 |
0,3 |
600 |
Поправочные коэффициенты при износе инструмента
В формулах для крутящих моментов указаны коэффициенты при нарезании резьбы не затупившимися метчиками и плашками. Когда износ инструмента достигнет предельной величины, указанной в таблице ниже, крутящие моменты рекомендуется увеличить: для метчиков в 2,5-3 раза, для плашек — в 1,5-2 раза.
Тип инструмента |
Схематическое изображение износа |
Величина износа δ в мм и расчетные формулы |
Примечание |
Автоматные гаечные метчики |
|
δ = 0,125d |
Для горячештампованных заготовок гаек |
|
δ = 0,05d |
Для травления и холодноштампованных заготовок гаек |
|
Гаечные метчики |
|
δ = 0,05d |
|
Машинные метчики |
|
δ = 0,125d δ = 0,07d |
Нарезка в стали Нарезка в чугуне |
Поправочные коэффициенты на скорость резания и крутящий момент для метчиков, плашек и резьбовых головок:
Обрабатываемый материал |
Поправочные коэффициенты на скорость резания в зависимости от |
Поправочный коэффициент КМр, на крутящий момент |
||
обрабатываемого материала KMv |
марки инструментального материала КИv |
|||
P6M5 |
9ХС; |
|||
Сталь: |
||||
Углеродистая: |
0,7 |
1,0 |
0,7 |
1,3 |
δв = 600 > 800 МПа |
1,0 |
1,0 |
||
Легированная: |
0,9 |
1,0 |
||
δв = 700 > 800 МПа |
0,8 |
0,85 |
||
Чугун серый: |
||||
НВ< 140 |
1,0 |
1,0 |
0,7 |
1,0 |
НВ 140-180 |
0,7 |
1,2 |
||
НВ> 180 |
0,5 |
1,5 |
Надеемся, эти советы помогут вам рассчитать правильный крутящий момент резьбонарезных цанг для предотвращения поломки инструмента и стабильного качества резьбы.